
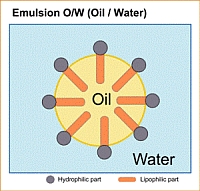
Depth-type absorbent filters made of inorganic media or metal should be used rather than paper or wood filters of the absorbent-surface type. Therefore, standard filtration methods used for petroleum hydraulic oils may not be satisfactory when using water-in-oil emulsions. As a result, invert emulsions are manufactured to a viscosity level somewhat higher than that of petroleum oils used in similar hydraulic applications.ĭue to their higher specific gravity, invert emulsions hold particulate contamination in suspension much more readily than does petroleum oil. For example, the Spans generally have low HLB numbers and they are also. W/O emulsions are generally formed if the aqueous phase constitutes < 45 of the total weight and an lipophilic emulsifier is used. These fluids exhibit a temporary reduction in viscosity when subjected to the high shear rates, which exist in most hydraulic pumps. Conversely, where water or aqueous solutions are dispersed in an oleaginous medium, the system is known as a water-in-oil (w/o) emulsion. Use unpainted reservoirs, as invert emulsions may have a solvent effect on paints and enamels, which cover the interior of some hydraulic reservoirs. The return-line discharge should be located as far as possible from the pump intake, and the fluid returned should be discharged below the lowest fluid level expected during operation. For this reason, larger reservoirs using adequate venting and baffles may be required. Generally speaking, most invert emulsions are compatible with standard hydraulic seal material and contain anti-wear additives and corrosion and rust inhibitors.įoaming and aeration can be greater problems with water-in-oil emulsions than with petroleum oils. Freezing temperatures can cause the emulsion to break. Heat exchangers may be required in some applications. System operating temperatures should not exceed 50 degrees C (122 degrees F) to reduce the possibility of water evaporation. Where possible, use distilled or de-ionized water to avoid introducing harmful contaminants that may cause emulsion problems. Therefore, it is extremely important that the percentage of water in the emulsion be monitored on a regular (daily) basis. If the water content is increased above 45 percent, the anti-wear characteristics of the fluid will be reduced. Generally, the percentage of water must remain between 35 to 45 percent, as these fluids begin to lose their fire-resistant properties at water levels of less than 35 percent. Maintenance of the water content of these fluids is critical. This type of fluid will have better lubricating abilities than a fluid that is 95-percent water and 5-percent mineral oil with additives, but will not be as fire resistant. Which type of solution is mixture of oil and water Solution is a homogeneous mixture of two or more components. These types of fire-resistant hydraulic fluids are often referred to as invert emulsions, which is to say, tiny droplets of water are suspended in the oil. Examples of oil-in-water emulsions include: mayonnaise and Hollandaise sauce (featuring egg yolk lecithin as the emulsifier), homogenized whole milk, and our vinaigrette dressing (described above). When oil is used as the main fluid and 40-percent water is added (emulsified) into the oil, it is described as a water-in-oil emulsion.
